Zhuang Xianguo
(Liaocheng Wanhe Industrial Manufacturing Co., Ltd., Liaocheng, Shandong 251022)
Abstract: From the working principle and structure of the tablet press, the components and causes of dust generation during the tableting process are briefly analyzed, and the solution to eliminate dust is proposed.
Key words: tableting dust; tableting production process; tableting dust generating parts; cause of tableting dust; method of eliminating dust
The "Good Manufacturing Practices" ( provisioned in 1998 ) issued by the State Drug Administration has made special provisions for pharmaceutical production equipment. Chapter 4, Article 31 “Design, selection, installation, etc. of equipment shall comply with production requirements, be easy to clean, disinfect or sterilize, facilitate production operation and maintenance, and prevent errors and reduce pollution.â€; Article 32 "The surface of equipment that is in direct contact with medicines shall be smooth, flat, easy to wash or disinfect, corrosion-resistant, and shall not chemically change or adsorb the produced medicines.". At present, the domestically produced rotary tablet presses are designed and processed according to the requirements of GMP . In the actual tablet production process, the press chamber often produces a large amount of dust for various reasons, thus causing the upper and lower punches. During the operation, the resistance increases, the upper and lower rail guides are damaged, the punching tail wears, and the electrical cabinet enters the dust to cause electrical failure.
In this paper, from the working principle of the rotary tablet press, the components and causes of the dust generated during the tableting process, the method of analysis and solution is established, and the dust removal method inside the rotary tablet press is established to reduce the dust pollution.
1 rotary tablet press working principle and mechanism
1.1 main structure
The working principle and structure of the rotary tablet press are shown in Figure 1. It is a widely used tablet press in the production, mainly consisting of transmission parts, turntable parts, upper and lower rail guide parts, pressure wheel frame parts, feeding Components, peripheral covers, etc.
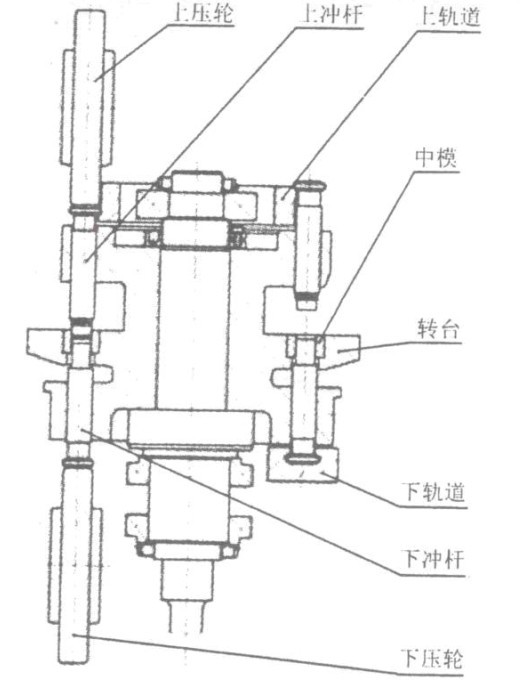
 figure 1   Rotary tablet press principle and mechanism
1.2 tableting workflow (see Figure 2)
The granular material falls into the feeder through the feeding hopper, and the turntable equipped with the upper punch, the lower punch and the middle die rotates one turn, and the up and down movement of the upper and lower punches is controlled by the upper and lower rail guides, the pressure wheel and the like, and the pressurization is completed. The process of filling, metering, tableting and filming of materials.
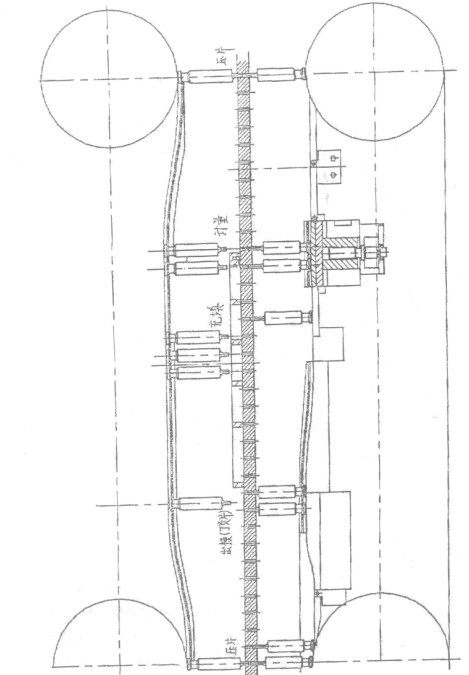
figure 2 Â Â Rotary tablet press workflow
2 main components and causes of dust generated by rotary tablet press
2.1 Dust generated during manual feeding
2.2 During the normal operation of the equipment, the generated dust is absorbed by the four plexiglass doors, and nothing can be seen clearly. In order to cope with the production, the plexiglass door has to be opened, which violates the GMP requirements. At the same time, the tail is also dusty. The dust will be adsorbed by the regularly-applied lubricant to cause oil shortage. If it is not cleaned in time, it will often cause the tail to be flushed. The rail guide is worn out and the equipment is not working properly. When the equipment is operated for a long time, the electrical cabinet enters the dust and cause electrical failure, which also pollutes the tableting chamber and is not easy to clean and disinfect the tableting chamber.
2.3 The dust generated during the normal operation of the equipment under the stamping process, although there is a suction nozzle, but the back of the bottom and bottom of the middle die will adhere to a certain amount of dust, remove the punch, and hit the middle die with a middle die. The attached dust enters the lower rail along the lower punching hole, and is mixed with the lubricating oil to form the sludge, and the environment for polluting the tableting chamber is not cleaned for a long time.
2.4 The fine powder leaked from the feeder in the normal operation of the equipment is not cleaned up in time, and the accumulation is small. As the turntable rotates, the gap between the turntable and the platen enters the lower rail guide, and the incoming dust will absorb the lubricating oil, causing the wear of the lower punch and the lower guide of the pressure wheel, reducing the service life of the rail guide. If it is found that it is not timely, there will be an interruption, which will damage the lower rail guide.
3 reduce the dust generated by the tableting process
3.1 Manual feeding method to reduce dust
3.3.1 Add a round cover with a handle to the upper mouth of the hopper, and cover it in time after manual feeding to prevent the dust from spreading.
3.1.2 Use a vacuum feeder to feed and seal the hopper.
3.2 The method of reducing the dust by pressing the punching operation
3.2.1 Increasing the auxiliary mechanism can adjust the depth of the upper punch into the middle die hole, and reduce the “puffing powder†when the tablet is pressed.
3.2.2 The suction nozzle of the single layer sucking the dust is changed to the double powder nozzle which can “pow the powder†when the punching film is sucked, and the fine dust on the plane of the turntable after the scraper is scraped.
3.2.3 Add a cover or cover on the upper opening of the slot to add a dust suction port to the powder suction nozzle to prevent the dust from spreading during the top film and the film.
3.2.4 Add a cover on the feeder
3.2.4 .1 force feeder, this approach is not adopted, but the feed hopper into the feeder port and forcing the powder outlet to seal soft spout is connected to the forced feeder hopper inlet conduit.
.2 3.2.4 NATURAL doser feeder grid above a plexiglass cover added to prevent the punch during operation of the dust particles generated by collision, while according to the depth of filling at different punch disposed downstream rail, to reduce the quantitative determination of particles Overflow.
3.2.5 Adjust the processing technology of the upper and lower punch holes and the middle mold inner hole of the turntable, improve the roughness of the inner hole surface and the circularity degree of the aperture, reduce the gap between the small head of the punch and the inner hole of the middle mold, and reduce the “puffing powder†and “ Leaking powder."
3.2.6 Add a dust removal interface on the top of the tableting chamber to further purify and reduce the dust in the tableting chamber.
3.3 Undershooting operation Tablets to reduce dust
3.3.1 Add the powder ring to the small head of the lower punch (see Figure 3 ), catch the dust when the next punching piece is caught, and then suck the dust on the powder ring by the powder suction nozzle to keep the body clean. It is also beneficial to lubricate the undershoot and extend the life of the turntable.
3.3.2 Remove the undershoot first when clearing the field, then use special cleaning tools to clean the dust under the middle mold. The dust falls on the powder ring, then sucks it off by the powder suction nozzle, removes the powder ring and unloads the middle mold.
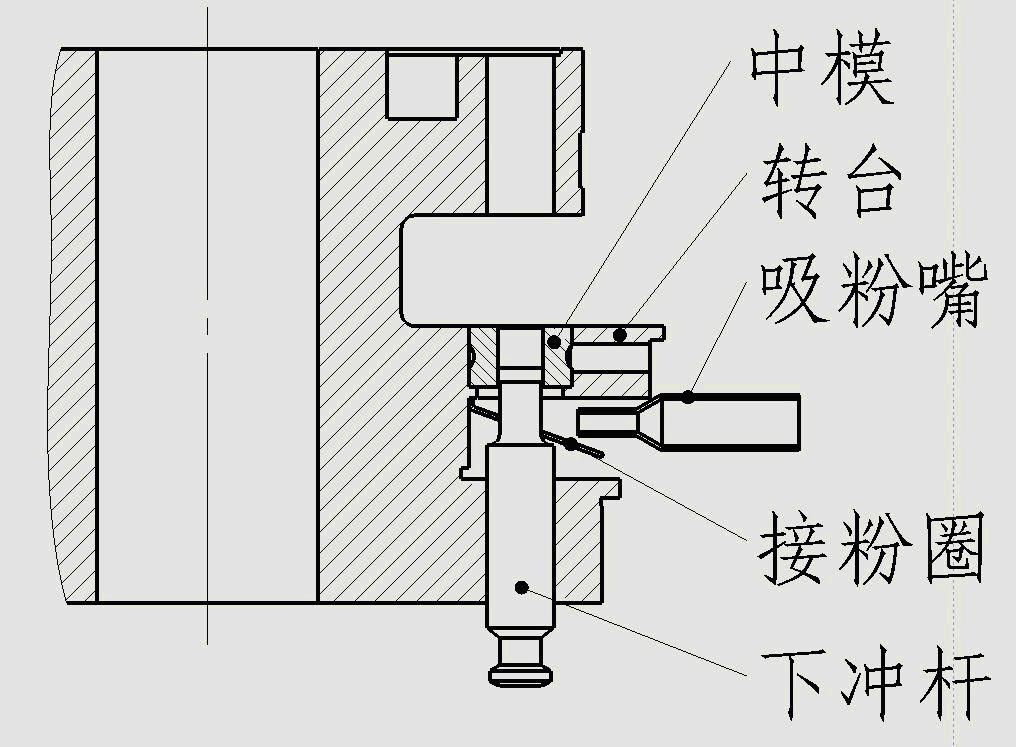
Figure 3 Schematic diagram of the powder ring
3.4 NATURAL feeder grid, forcing the plane of the bottom surface of the feeder turret mold are present in the case where the turret during tableting powder leakage outside the park
3.4. Single raster does not change the basic structure of the feeder, reducing the wall thickness, forming the backbone of the feeder, and then spraying or casting polytetrafluoroethylene.
3 . 4 . 2 forced feeder to change the copper substrate hopper to a polyurethane seal structure.
3 . 4 . 3 The feeder becomes a gapless feeder. The bottom of the feeder is in zero gap contact with the die table in the turntable, which eliminates the structure of the scraping board, avoids powder leakage of the powder in the outer circle of the turntable, and avoids leakage of powder. Excessive dust enters the undershoot, which is more conducive to maintaining the consistency of the weight.
4. Conclusion
Through the above improvement measures, the amount of dust will be greatly reduced, basically solving the damage caused by dust, and the electrical leakage caused by dust entering the electrical cabinet, and there will be a small amount of dust in the tableting chamber.
Absorbable Haemostats Products
Absorbable Haemostats,Haemostatic Absorbable Sponge,Haemostatic Absorbable Gelatin Sponge,Absorbable Hemo Haemostatic Gauze Pad
Shaoxing Aladdin Enterprise Co.,Ltd , https://www.xhemostat.com